Heat treatment of steel is a controlled process of heating and cooling steel to alter its microstructure and mechanical properties.
This process is used to achieve desired characteristics such as increased hardness, strength, toughness, wear resistance, or ductility.
The three major heat processes worked at OMVP are annealing, through and local hardening, case carburizing.
This process is used to achieve desired characteristics such as increased hardness, strength, toughness, wear resistance, or ductility.
The three major heat processes worked at OMVP are annealing, through and local hardening, case carburizing.
- Annealing is applied to steel to improve its mechanical and microstructural properties. The primary goals are to soften the material, enhance ductility, relieve internal stresses, and refine the grain structure. Annealing is often performed on steel that has been subjected to high stresses during manufacturing
- Through hardening (also known as quench hardening) is a heat treatment process used to increase the hardness and strength of steel throughout its entire cross-section
- Local hardening is a heat treatment process applied selectively to specific areas of a component to increase the hardness and wear resistance of those areas while leaving the rest of the material unaffected. This process is used when only certain regions of a part require enhanced mechanical properties
- Case carburizing is a heat treatment process used to harden the surface layer of steel components while maintaining a tough and ductile core. This process introduces carbon into the surface layer of low-carbon steel parts, enabling the creation of a hard, wear-resistant outer layer after quenching, while the core remains softer and more impact-resistant
- 2 x Annealing furnaces of whereof 1 is in controlled atmosphere
- 13 x furnaces for Martensitic Hardening by belt, rollers and baskets
- 2 x furnace for Case Carburizing
- 1 x furnace for Local Hardening
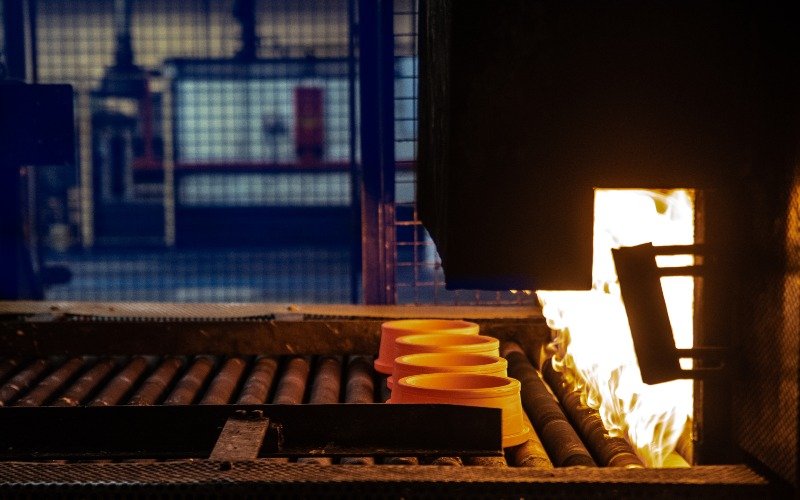
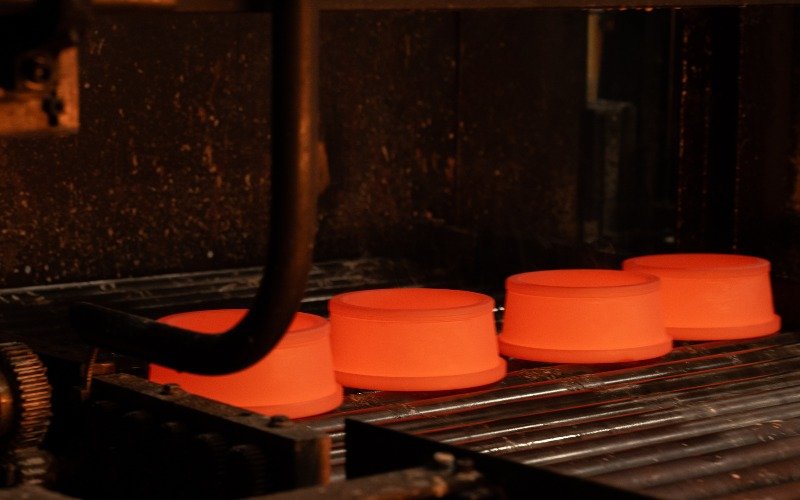
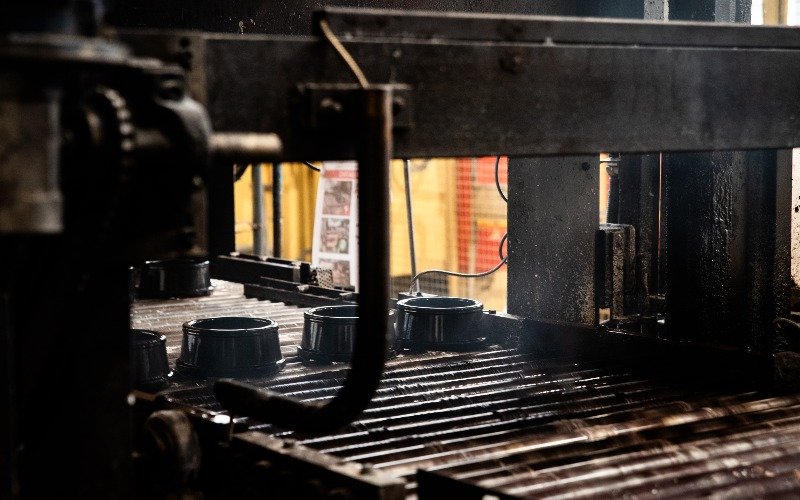
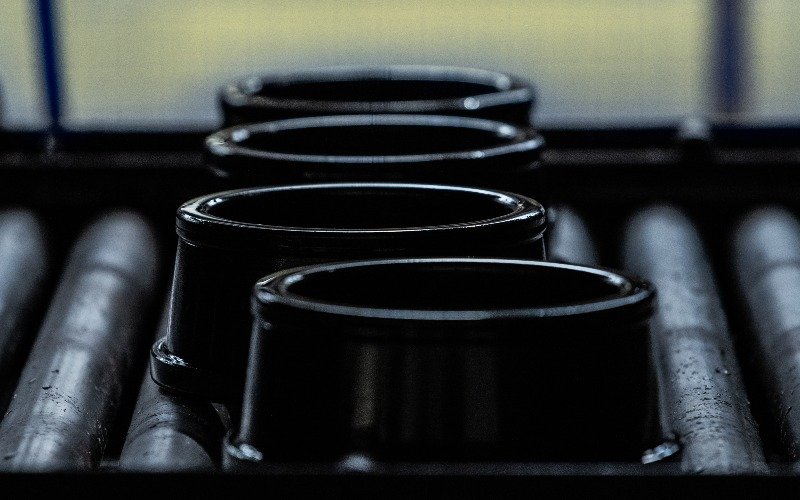
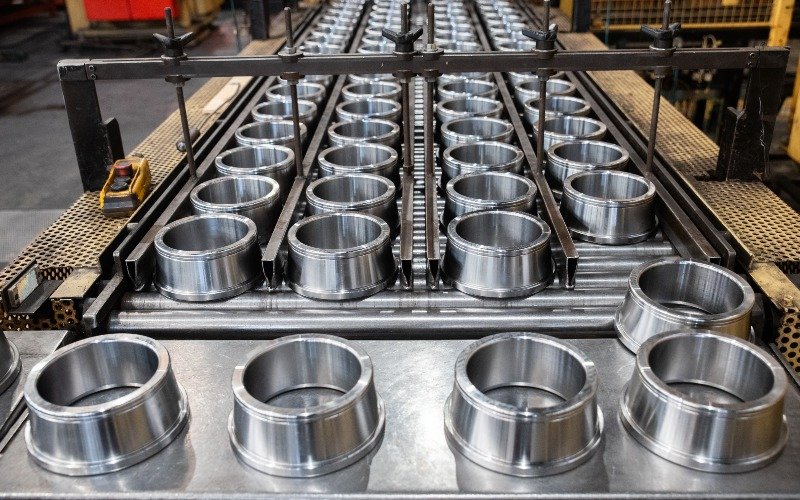
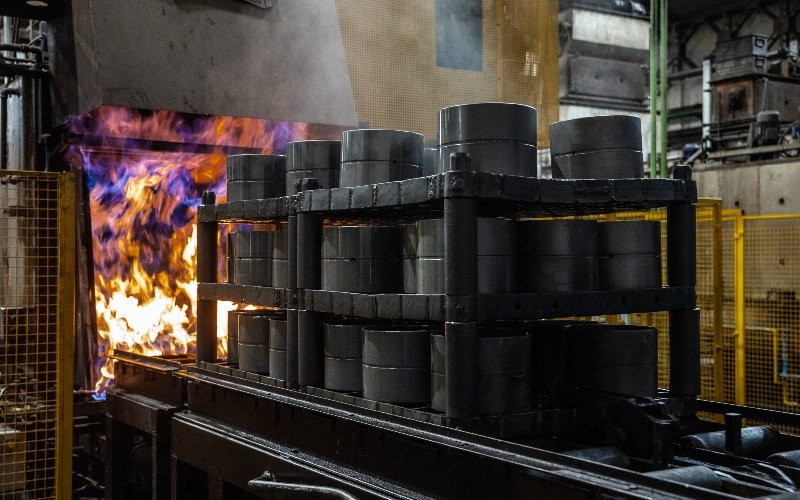
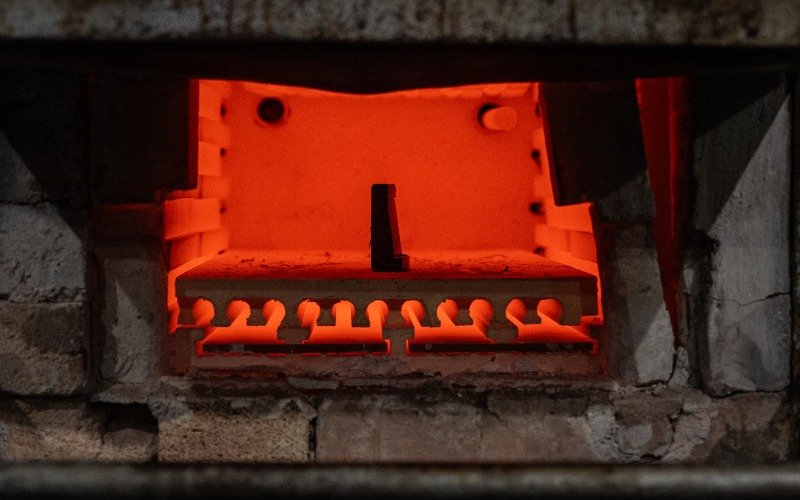
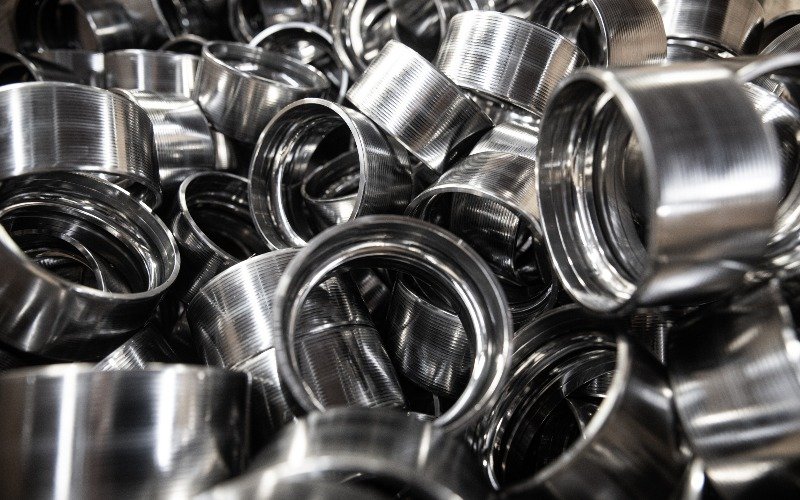
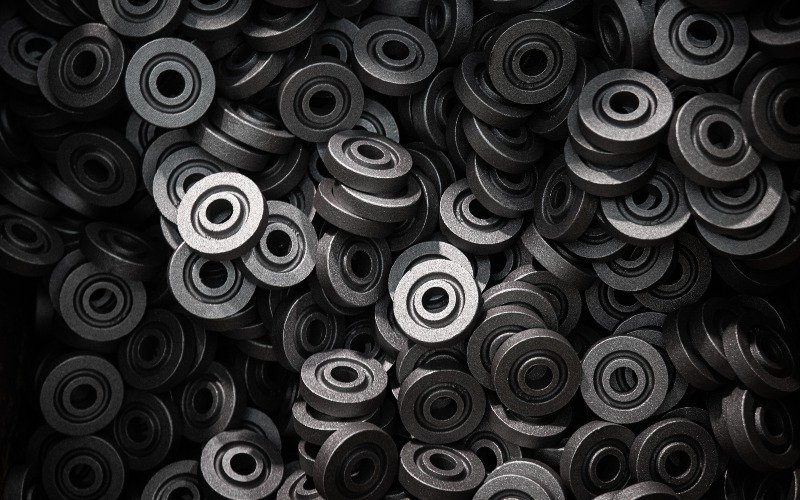